SAUBER C-9. Swiss race car constructor Peter Sauber built his first Group C car, the C6, in '82
- Sergio Goldvarg
- Nov 21, 2014
- 9 min read
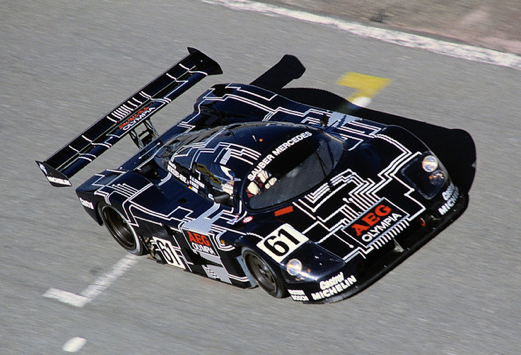
A Chevrolet powered version of the C7 was subsequently seen in IMSA in '84, during which season Sauber asked permission to use the Daimler-Benz wind tunnel at Unterturkheim, the marque's Stuttgart home. The contact between Sauber and the Daimler-Benz R&D department led to con-sideration of a Mercedes V8 turbocharged Group C engine. Sauber had seen the po-tential of the all alloy, chain driven s.o.h.c., 16 valve M117 engine as the base for a powerful and reliable turbocharged Group C power plant. The M117 was the latest in a succession of Mercedes V8 engines stretching back to 1963. The original 6.3 (later 6.9) litre V8 had been followed in 1969 by a new generation 3.5 litre M116 V8 from which the M117 was directly descended. The M116 had iron block and alloy heads with chain driven s.o.h.c. Its two valves per cylinder were offset 20 degrees from the vertical in a wedge-shaped combustion chamber surrounded by generous squish area, run in conjunction with a flat topped piston. Although the offset valves were set in parallel they were operated through fin-ger cam followers which pivoted on spheri-cal-headed adjuster studs. The M116 en-gine was taken out to 4.5 litres then, 10 years after its introduction, was replaced by the alloy block M117. While the M117 generally followed the pattern of the iron block engine (retaining the wedge heads) the important difference was a massive weight saving in the order of 125kg. This was made possible through a new production technique offering a liner-less block, as pioneered by General Motors with the famous Vega 2300 engine. The linerless block was diecast by the new `Accurad' method in a new aluminium alloy, Reynolds A390, which combined good flu-idity in the molten condition with a fine dispersion of silicon after heat treatment giving good bearing properties and ease of machining. After machining an electro-chemical etching process was used to expose the hard silicon particles on the walls providing a wear resistant and oil retaining surface which was used in con-junction with an iron-plated piston skirt (reversing the usual combination of alloy piston on iron bore). Though the production M117 engine was not turbocharged, the research engineers at Stuttgart were already familiar with the challenge of forced induction, having worked with turbocharged engines for 15 years. However, Damiler-Benz AG was riot yet ready for a direct involvement in motor racing so the parts and technical information were supplied to Heini Mader who built the first twin turbo Mercedes Group C engine. The project echoed that of Aston Martin, on behalf of which Tickford had toyed with a short lived Group C V8 turbo engine early in '84. The Mercedes challenger was a superficially similar, large capacity, lightly blown 90 degree V8. Likewise, it was es-sentially stock and consequently had a two plane crankshaft for smooth running.
The two-plane configuration made for a very smooth engine at the expense of exhaust tuning potential. However, that was not a serious concern given forced induction and
Rear end view of the Mercedes V8 M117 all alloy engine with twin KKK turbochargers. The unit ran a Motronic engine management system.
The smooth, well balanced nature of the unit was considered ideal for an endurance car. The prototype engine first ran on the dyno around Christmas '84 and started track testing in March '85. Initially the head gas-ket gave problems but once the Stuttgart engineers had solved this it ran well. The solution was in a modified gasket and a stiffer head, the latter involving a modifica-tion to the casting which was carried through to the production car line. The Mader engine benefitted from a dry sump, porting and camshaft work, in-creased water circulation, special heat resistant valves and oil sprayed pistons. Type 27 turbochargers were supplied by KKK and these were goverend by mechani-cal wastegates which were modified Por-sche road car items. The appropriately revised induction system included air:air aftercoolers while injection and ignition were incorporated in the Porsche Group C-type Motronic M1.2 package which was supplied by Bosch. Daimler-Benz had worked closely with Bosch for many years.
Together they had pioneered fuel injection for road car engines and engine manage-ment systems. The Mader-assembled 5.0 litre Mercedes engine was pressurized to a maximum of 2.0 bar absolute in qualifying, at which power was in excess of 700bhp. Race boost was 1.8 bar absolute while for maxi-mum power the drivers had to look no further than 6,600rpm. Sauber went in at the deep end, the Mer-cedes-Sauber C8 debuting at Le Mans. Qualifying was encouraging until, warming up for a serious attempt to post a grid time, it took off over the brow after the Mulsanne kink. It somersaulted a couple of times and was wrecked, thankfully without injury to driver Nielson. Daimler-Benz kept faith with Sauber and a short, five-race programme was undertaken in '86, highlighted by vic-tory in the wet at the Nurburgring, aided by the tremendous torque of the low revving, big displacement engine. In the dry the Mercedes-Sauber was less impressive but with continuing engine development work and an improved chassis, the C9, in 1987 the package was a real contender. Again the season was only five races long and this time the highlight was pole at Francorchamps.
For 1988 Daimler-Benz came out and gave the effort factory support for a full season and en-gines were supplied directly from Stuttgart. The commitment was immediately re-warded with a win at Jerez. Following a disappointing withdrawal from Le Mans in the wake of unexplained tyre blow outs, the team bounced back to win at the Norisring and Brno. Over the Mader seasons the key engine developments were the introduction of Nikasil coated bores, a new lighter crank-shaft, improved, higher efficiency turbo-chargers and a switch to the Motronic M1.7 engine management system offering more precise control of ignition and injection, plus electronic control of a new wastegate. In addition, a total of 20kg. was saved through lighter internals (including titanium con rods), a lighter flywheel, lighter ancillaries and lighter turbochargers. Even the cam-shafts were lightened, through a new form of construction. With the more precise ignition control of the M1.7 system the compression ratio could be increased from an initial 8.0:1 to 8.5:1 while power was then officially 700bhp/7000rpm on the 1.9 bar absolute race setting. In qualifying almost 800bhp was extracted. Nevertheless, the base engine remained essentially a production item. M117 race engines were built from production castings which had been taken from the factory and sent to Mahle for a conventional Nikasil coating to be applied to the bores. The linerless M117 block extended below the crankshaft axis to allow side as well as vertical bolting of the full-width main bear-ing caps. The four-bolt caps for the five bearings were of cast iron while the race engine's bespoke dry sump (attached via stock studs) was of magnesium and was designed to accept chassis loads. The engine was semi-stressed with loads also fed into the heads. The ported alloy heads were attached by six bolts per cylinder and the valve gear was mounted directly on the head. An aluminium rocker cover was re-tained from the production engine. The two-plane crankshaft ran in 64mm. diameter plain bearings supplied by Glyco and while lighter than standard was to the same design with the same balancing webs and journal sizes. An in-house production, it was of forged steel and was only polished, receiving no special treatment. As the production crankshaft, the race crank was fitted with a harmonic dampener but this was of a different design in view of the higher revs sought. It was supplied by Goetze. The flywheel was steel, attached by eight bolts and was sized to match a standard 71/4 inch clutch with a starter ring around it. The crankshaft was driven by titanium con rods through 48mm. diameter plain Glyco bearings. The fully machined con rods were of (-section and were supplied by Pankel in Austria. At 170.5mm. eye to eye they were a little longer than standard for a shorter, lighter piston. The Mahle piston was at-tached by a conventional steel gudgeon pin with circlips and was of the oil gallery type, fed by a single jet.
The production head's wedge shaped combustion chamber was retained, the parallel valves inclined to one side with the plug reaching in on the other. The race engine differed only in a dish in the piston crown reducing the compression ratio from the stock 10.0:1. The piston carried three cast iron rings, of which the top was chrome plated. The smaller, lighter piston carried smaller than standard rings. American supplier TRW provided the rings at Mahle's recommenda-tion. The special head gasket resembled that of the production car and was supplied by German company Reinz. The head was fitted with Stellite seats for both inlet and exhaust valves which ran in bronze guides. The valves were steel with a Nimonic foot and on the exhaust side were sodium cooled. Dual steel springs were fitted under a titanium retainer.
The Pescarolo/Danner/ Quester Sauber-Mercedes lasted only 86 laps of the 1986 Le Mans race, 25 more than its sister car. Both suffered engine failures.
The production valve gear was retained, with the finger cam followers reducing side loading compared to direct operation of the parallel valves by the cams. However, for the race engine the hydraulic piston atop which the follower's pivot was mounted to provide automatic adjustment was re-moved, replaced by a mechanically-ad-justed stud. The only other modification was a specially hardened plate which was soldered to the top of the steel follower to form the cam working surface. The camshaft had journals of large enough diameter to allow it to be inserted through bearing holes in aluminium shaft supports, five of which were were bolted to each head. The steel shaft ran directly in its supports and was of a newly devised built-up type produced by a Mahle subsidiary. The method was to produce the cam lobes and the journals separately then to slide them onto the tubular base shaft under a heat process. The resultant shaft was reck-oned to be lighter and was less expensive to produce. The camshafts were driven by a chain off a sprocket at the front of the crank. The double-row chain was a production item and was fitted with a tensioner. Between the front main bearing and the timing drive sprocket was another sprocket, this one to drive the oil pressure pump which was mounted inside the front cover. The scav-enge pumps were mounted outside and were driven by a belt from a pulley on the nose of the crank. In fact there were two pullies, a second belt driving the water pump and alternator. The water pump was set into the front cover in a central position while the scav-enge pumps were to the left of the crank-case, the alternator to the right. Of the five scavenge pumps, three served the engine, two the turbos. Compared to the production engine the dry sump race unit had improved water circulation through enlarged chan-nels - particularly in the head - with twice as much water in circulation. The alternator was supplied by Bosch, which had developed a distributorless igni-tion system for the engine. Until mid '87 it ran with a conventional flywheel triggered Bosch CD system. However, with the M1.7 system, this was replaced by a multi-coil system, the coils triggered by the ECU which took impulses from the flywheel and a camshaft sensor.
Rather than having a coil for each plug, one coil jointly served two cylinders and consequently each plug was fired twice per four stroke cycle. This was not, however, found to adversely affect performance. As for the production engine, the firing order was 1-5-4-8-6-3-7-2. Fuel was injected into the ports rather than the inlet trumpets. The fuel injectors were screwed into the head, as on the production engine, one injector per cylinder. In spite of this arrangement atomization was consid-ered adequate, "with the valve mostly re-sponsible for atomization, anyhow", ac-cording to Development Engineer Withalm. Earlier the engine had run two injectors per cylinder with the second operating only at full throttle. However, improved injector design and improved control via the switch from M1.2 to M1.7 Motronic had allowed one to be dispensed with. Two throttles were fitted, one just ahead of each entry to the plenum chamber, each turbocharger blowing through its own after-cooler. The inconel turbine turbochargers featured no trickery and had essentially remained unchanged throughout the en-gine's career. With the M1.7 system Daim-ler-Benz produced it own wastegates for electronic control throughout the rev range via the ECU. The driver remained in overall charge of the maximum boost pressure.
The Motronic ECU took readings, apart from those of the crankshaft and camshaft sensors, of charge air pressure as felt in the plenum, air and exhaust gas temperature, water temperature, oil temperature and pressure, fuel temperature and pressure and even turbocharger r.p.m. However, the system retained a plug-in EPROM, unlike the Zytek system used by Jaguar. It was used in conjunction with a telemetry system on race day, allowing the engineers to monitor temperatures and pressures. The map provided for the engine in 1988 was based on reference points at 500rpm and 0.1 bar intervals. By 1988 Daimler-Benz had produced around 30 race engines. Each was reck-oned to take two persons one week to strip and rebuild. There were no special qualify-ing engines but on 2.2 bar absolute qualify-ing power was rated as "almost 800bhp". Maximum revs were 7,000 but the driver was asked to observe a limit of 6,500 on race day, aside from overtaking. At the 1.9 bar absolute race setting torque was a massive 800n.m. at 4250rpm and the torque band was spread all the way from 3,000 to 6000rpm: sheer grunt was this unit's great strength.
Le Mans 1987 - Peter Sauber and crew attend the rapid Thackwell car. Constructor Sauber is holding the passenger door, while Thackwell awaits his turn.
Comments